Wire angle correspondance
Straight Track Moller Rates
Goal: Confirm that the moller Rate (Hz) seen in on a wire agrees with the Rate calculated from the cross section. The torus is turned off so the wire is more easily correlated with the moller scattering angle. No need for track reconstruction.
Determining wire-theta correspondence
To associate the hits with the Moller scattering angle theta, the occupancy plots of the drift chamber hits by means of wire numbers and layer must be translated using the physical constraints of the detector. Using the data released for the DC:
DC: Drift Chambers(specs)
DC Geometry(geom)
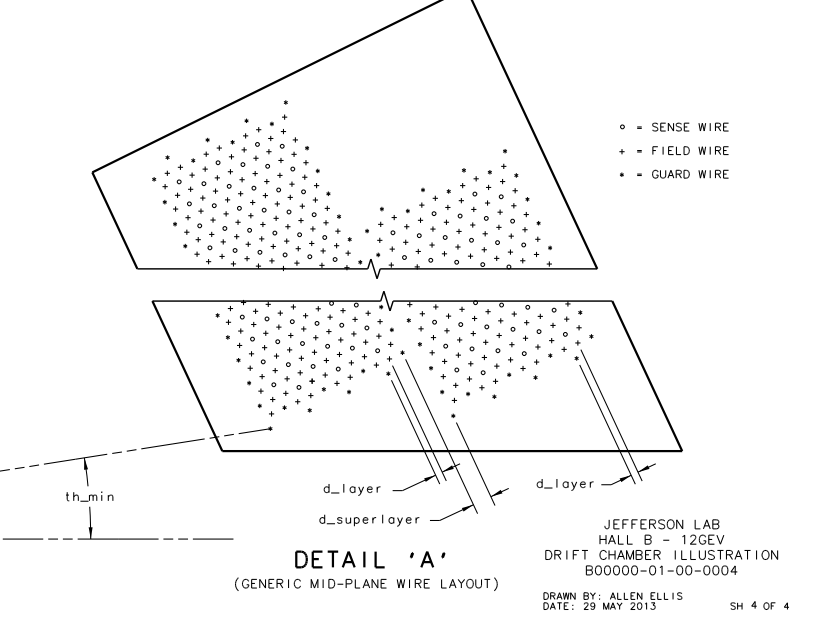
Examining the geometry file, we can see that each plane, not just the plane of the sense wires, is separated by a distance of D=.3861 cm. We can use the geometry of the wire placements to find
Finding the separation distance between two adjacent sense wires
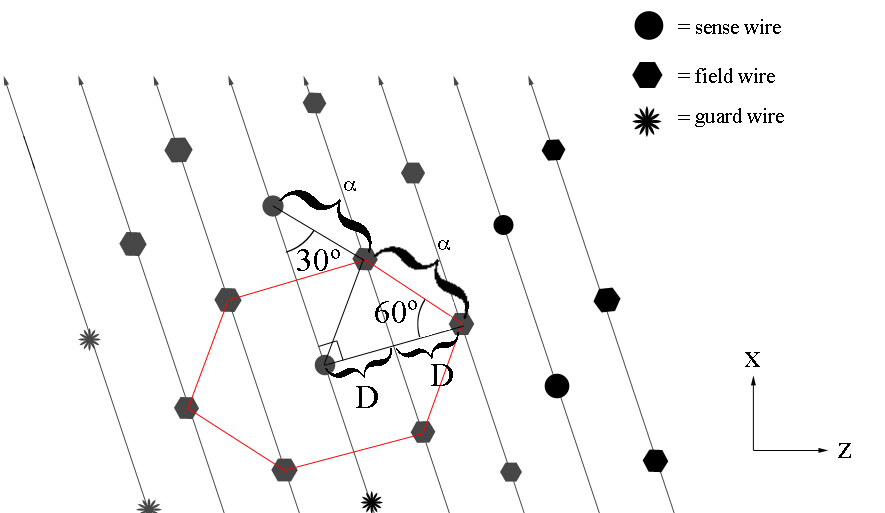
Since the separation between adjacent sense wires is uniform and at a set angle of 25 degrees with respect to the beam line, we can use this fact to determine the angle theta each wire makes when measured from the vertex.
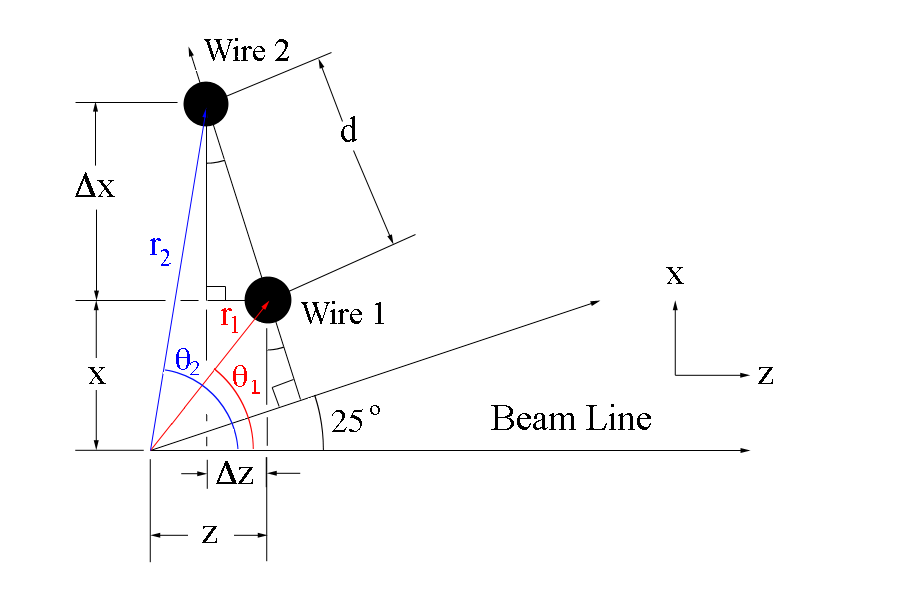
The new x and z coordinates for wire 2 can be found using the change in the components
This can be extended to any point along the same wire plane, starting from the coordinates for wire 1
The angle theta that the wire makes with the vertex is given by
CED Verification
Using CED to verify the angle and wire correlation,
Zooming in on the view paralell to the direction of the wires in ced, we can examine the wire corresponding theta angle in the drift chamber.
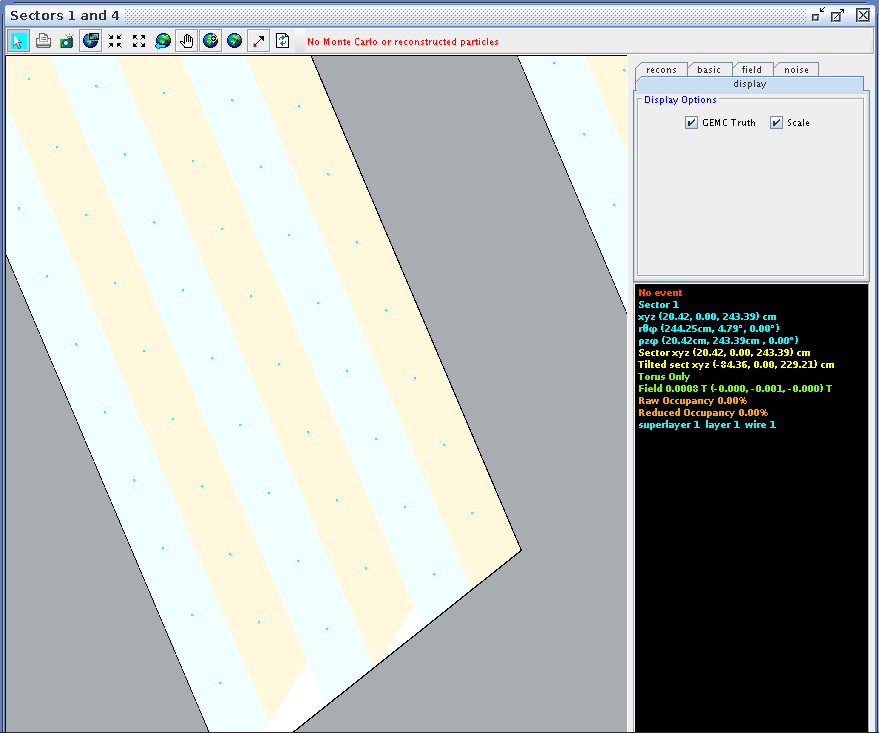
Coordinates(cm) | Layer 1 | Layer 2 | Layer 3 | Layer 4 | Layer 5 | Layer 6 |
---|---|---|---|---|---|---|
x | 20.42 | 21.51 | 21.39 | 22.49 | 22.37 | 23.47 |
y | 0.00 | 0.00 | 0.00 | 0.00 | 0.00 | 0.00 |
z | 243.41 | 244.18 | 245.51 | 246.28 | 247.62 | 248.38 |
Coordinates(cm) | Layer 1 | Layer 2 | Layer 3 | Layer 4 | Layer 5 | Layer 6 |
---|---|---|---|---|---|---|
x | 21.64 | 22.73 | 22.61 | 23.71 | 23.58 | 24.69 |
y | 0.00 | 0.00 | 0.00 | 0.00 | 0.00 | 0.00 |
z | 242.86 | 243.62 | 244.94 | 245.71 | 247.05 | 247.81 |
Corresponding theta angles can be found for other wires, in Region 1, Superlayers 1 and 2.
Wire Number | Layer 1 | Layer 2 | Layer 3 | Layer 4 | Layer 5 | Layer 6 |
---|---|---|---|---|---|---|
1 | 4.79 | 5.03 | 4.98 | 5.22 | 5.16 | 5.40 |
2 | 5.09 | 5.33 | 5.27 | 5.51 | 5.45 | 5.69 |
62 | 24.42 | |||||
63 | 24.76 | |||||
64 | 25.10 | |||||
77 | 29.46 | 29.60 | 29.41 | 29.55 | 29.37 | 29.51 |
78 | 29.79 | 29.93 | 29.74 | 29.88 | 29.69 | 29.83 |
79 | 30.12 | 30.26 | 30.07 | 30.21 | 30.02 | 30.16 |
110 | 40.19 | 40.28 | 40.05 | 40.13 | 39.91 | 39.99 |
111 | 40.51 | 40.59 | 40.36 | 40.44 | 40.21 | 40.29 |
112 | 40.82 | 40.90 | 40.67 | 40.75 | 40.52 | 40.60 |
Wire Number | Layer 1 | Layer 2 | Layer 3 | Layer 4 | Layer 5 | Layer 6 |
---|---|---|---|---|---|---|
1 | 4.79 | 5.03 | 4.98 | 5.22 | 5.16 | 5.40 |
2 | 5.09 | 5.33 | 5.27 | 5.51 | 5.45 | 5.69 |
77 | 29.46 | 29.60 | 29.41 | 29.56 | 29.37 | 29.51 |
78 | 29.79 | 29.93 | 29.74 | 29.88 | 29.70 | 29.84 |
79 | 30.13 | 30.27 | 30.07 | 30.21 | 30.02 | 30.16 |
110x | 40.19 | 40.28 | 40.05 | 40.13 | 39.91 | 39.99 |
111 | 40.51 | 40.59 | 40.36 | 40.44 | 40.22 | 40.30 |
112 | 40.82 | 40.90 | 40.67 | 40.75 | 40.52 | 40.60 |
Super Layer 1:Layer 1
Coordinates(cm) | Layer 1 | Layer 2 | Layer 3 | Layer 4 | Layer 5 | Layer 6 |
---|---|---|---|---|---|---|
1.22 | 1.22 | 1.22 | 1.22 | 1.21 | 1.22 | |
0.00 | 0.00 | 0.00 | 0.00 | 0.00 | 0.00 | |
.55 | .56 | .57 | .57 | .57 | .57 |
Using the geometric construction for determining angle theta to wire 2:
This equation can be solved for a hypothetical wire 0, which will allow the wire number to be the multiplicative factor for the change from the starting position.
where
Using Mathematica, a series expansion about n=0 can be found:
In[1]:= Series[ArcTan[(19.21+1.212 x)/(243.39-0.5652 n)],{n,0,4}] Out[1]= 0.0787635+0.00513098 n+9.83726*10^-6 n^2-2.61675*10^-8 n^3-2.22826*10^-10 n^4+O[n]^5
This expression will find the angle theta in radians given the wire number. To convert from radians to degrees, we can multiply by 180 and divide by Pi.
In[2]:= 180*(0.07876354504106763`+0.005130982891104289` n+9.837257652182922`*^-6 n^2-2.616751708660921`*^-8 n^3-2.2282595631625944`*^-10 n^4+O[n]^5)/3.14159625359 Out[2]= 4.51281+0.293983 n+0.000563633 n^2-1.49929*10^-6 n^3-1.2767*10^-8 n^4+O[n]^5
This tells us that the expression for theta will follow a function that comes from a series expansion. To account for instrument and measurement errors, angle measurements from ced can be used to find a better fit.
Using Mathematica, a line can be fitted to the data collected on the wire number to angle theta correspondence.
Declaring the data set:
In[1]:= data1={{1,4.79},{2,5.09},{62,24.42},{63,24.76},{64,25.10},{78,29.79},{111,40.50},{112,40.82}} Out[1]= {{1,4.79},{2,5.09},{62,24.42},{63,24.76},{64,25.1},{78,29.79},{111,40.5},{112,40.82}}
Testing for a linear fit:
In[2]:= line1=Fit[data1,{1,n},n] Out[2]= 4.39975 + 0.32469 n
Examing the range limits for the angle theta for layer 1:
Taking the difference of the upper and lower limits in theta,
Dividing by the change in wire numbers (112-1=111), we find
This would imply that if the wires were evenly placed, their change in angle theta would increase by the factor of .325 degrees for each increase in wire number, starting obviously with wire 1 at 4.79 degrees. In addition, this implies that the bin spacing for each wire would be around .325 degrees in width.
Chercking this, we can find the difference between wires 1 and 2,
Similarly, finding the difference between wires 111 and 112,
These differing values show that the bin width is not uniform in length, therefore a first order, linear fit, will not suffice.
Testing for a quadratic fit:
In[3]:= quad1=Fit[data1,{1,n,n^2},n] Out[3]= 4.45564 +0.32015 n+0.0000417787 n^2
The quadratic fit does not work since it's first derivative
does not give the same spacing between low and high values of n as seen in the ced data. The coefficient near the first order will have to smaller than .31 to find a correlation that would agree.
Testing for a polynomial of degree 3 fit:
In[4]:= polynomial1=Fit[data1,{1,n,n^2,n^3},n] Out[4]= 4.49876 +0.293001 n+0.000679074 n^2-3.57132*10^-6 n^3
This fit best matches the data found in ced
As discussed earlier, taking the 1st derivative of this function will give us the spacing of the bins as a function of wire number.
The derivative of this function then will tell us where the bin spacing is at a minimum and a maximum.
Comparing this maximum, we can see from Table 3 that near the maximum of 63 are seperated by larger distances than at n=1 or n=112.